Développement durable, depuis 1870.
Développement économique durable.
Ateliers François S.A. fut fondée à Liège en 1870, depuis ses différentes activités dans le domaine de l’air comprimé à travers les siècles, AF Compressors est, à ce jour et depuis 20 ans, le leader mondial des compresseurs à pistons sans graissage destinés à l’industrie du soufflage PET.
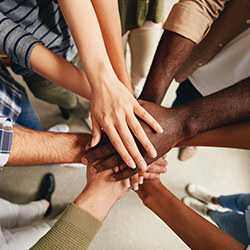
1) RSE, Responsabilité Sociétale de l’Entreprise.
Ateliers François S.A., une entreprise à taille humaine.
La gestion du personnel, plus globalement la gestion sociale au sein d’Ateliers François S.A. est solidement établie sur les législations en vigueur en matière de pratiques sociales et d’emploi, que ce soit au niveau national ou international.
La diversité présente au sein du personnel en termes d’origine, d’âge, de genre et d’opinion rencontrent les valeurs de tolérance, de bien-être au travail. Ces valeurs rejettent formellement toute forme de discrimination ; le harcèlement ou l’intimidation dans l’entreprise.
La diversification est aussi valorisée par ressources humaines, le recrutement, par les compétences, les expériences professionnelles complémentaires. Les responsabilités sont établies en fonction des objectifs personnels et communs. L’esprit d’équipe, l’initiative, la flexibilité, sont encouragés par le département des ressources humaines. Le cadre de travail, l’ergonomie comme la politique de santé de sécurité, sont essentiels au bien-être du personnel au sein de l’entreprise. AF veille au bon respect du bien-être social ainsi que des règles en vigueur au sein de son organisation comme dans le suivi de la chaîne d’approvisionnements et logistique au niveau international.
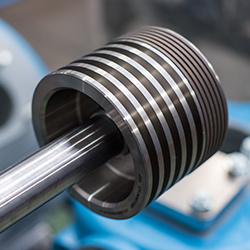
2) Développement économique durable.
Déjà, depuis les années 1980, la société a continuellement développé sa gamme de compresseurs d’air en optimisant le design mécanique, la technologie pour des rendements meilleurs d’une part, comme pour la facilité de maintenance de ses équipements. L’enjeu vise la réduction de ces coûts que ce soit par la réduction des consommations énergétiques ou par la réduction des pièces de rechanges.
En réponse aux besoins des clients pour plus de technologie toujours plus orientée vers la durabilité des équipements, que ce soit en applications 20-40 bar et surtout en applications basse pression 7 bar et 10 bar, AF poursuit ses investissement en Recherche et Développement en améliorant l’efficacité des produits, réduisant ainsi leur impact carbone.
Vers 2010, AF Compressors a encore intégré la technologie éprouvée du piston sans graissage, design en L caractéristique d’Ateliers François pour les compresseurs 40 bar, dans l’application d’air standard sans graissage oil-free, pour des pressions de 6 à 15 bar. En réalité, ce développement outrepasse les attentes des clients en matière d’économie d’énergie, de coûts de maintenance réduits et de longévité de durée de vie des équipements. Ces observations positives sont aussi vérifiées sous des conditions d’utilisation extrêmes, qu’elles soient désertiques, à 50°C, ou en milieu tropical chaud et humide.
La tendance sur le marché de l’air comprimé à travers le monde s’oriente vers une qualité d’air toujours plus haute. De plus en plus d’applications comme d’utilisateurs font le choix d’une qualité d’air comprimé ne présentant aucun résidu ni contaminant d’aucune sorte ; technologie sans graissage ou à marche sèche, sans résidu d’hydrocarbure ni d’huile, avec un point de rosée toujours maîtrisé. Cette qualité d’air est nommée Classe 1 selon la norme standard ISO 8573-1. La classe 1 présentant des caractéristiques mesurables en pratique, est la référence de qualité d’air pour l’industrie alimentaire.
Si la tendance des marchés s’oriente clairement vers des standards de qualité d’air très pointus, les exigences particulières en matière de développement durable et de Sustainability ne sont pas en reste. « Sustainability », ou la durabilité en matière d’air comprimé peut être exprimée par :
– la consommation énergétique de l’installation d’air comprimé à travers toutes les conditions d’utilisation (100% en charge, en charge partielle ou à vide), les consommations engendrées lors sa production, ainsi que la durée de vie et d’utilisation de cette installation à travers le temps.
Au fil des années cependant, le coût de l’air comprimé augmente, que ce soit par le coût d’acquisition des équipements ou les coûts liés au fonctionnement de ceux-ci, tout comme les coûts de fonctionnement de ceux-ci. Avec le changement climatique et ses conséquences, le coût de l’électricité risque de continuer à augmenter inexorablement, par une offre plus limitée et une demande sans cesse grandissante.
Consommation énergétique et empreinte carbone.
80% des dépenses opérationnelles de l’air comprimé dans le monde concernent l’électricité. La consommation énergétique est exprimée en Consommation d’Energie Spécifique (CES) d’un compresseur. Un compresseur d’air travaille complètement en charge ou en charge partielle. Très peu de compresseur d’air tournent continuellement en charge. Il est bien reconnu qu’en charge partielle bon nombre de compresseurs perdent énormément d’énergie. La Variation de Fréquence ou le « VSD » n’élimine pas totalement les pertes liées à la charge partielle, car souvent, les performances ne sont pas à la rencontre des chiffres espérés. De plus, des pannes coûteuses et une durée de vie limitée de l’électronique doit être prise en compte.
L’innovation réalisée par AF Compressors dans le domaine de l’air comprimé sans graissage est dans la conception même d’une nouvelle génération de compresseurs oil-free à pistons, de puissances de 90-110-132kW. L’efficacité de ces nouveaux modèles, présente également un rendement énergétique supérieur, alors qu’en charge partielle, ils ne présentent encore que très peu de pertes. Les OPC90-110-132 demeurent avec une puissance spécifique en dessous de 7kW/m³/min, alors qu’en charge, ils comptent parmi les compresseurs les plus efficaces avec seulement une consommation de 5,5 kW/m3/min à 8 bar. De cette manière, la gamme OPC90-110-132kW se situe 29% en dessous des valeurs requises par l’organisme allemand BAFA, (Bureau Fédéral des Affaires Economique et Contrôle des Exportations) Cet organisme subsidie les projets sensibles au niveau énergétique en Allemagne, d’autres organismes similaires, dans d’autres pays, répondent à ces mêmes critères.
La plupart des compresseurs secs lorsqu’ils tournent à vide ou partiellement en charge voient leur consommation atteindre des valeurs allant de 8 à 9kW/m³/min.
Le système à charge partielle (AFS – Adjustable air-Flow System) assure un contrôle optimisé du débit sur une plage de pression réduite. Grâce à ce contrôle digital, ces machines sont gérées comme deux unités en une. Dans certains cas, ceci rend l’utilisation d’un variateur de fréquence superflu voire directement évitable. L’économie d’une électronique parfois coûteuse et dont la durée de vie est souvent limitée peut alors être réalisée.
Ateliers François oriente ses Recherches et Développements dans le sens de l’économie de matière, de consommation énergétique, tels que par le passé déjà le système de récupération d’air « Air back », ou plus récemment les systèmes de gestion, les systèmes de récupération de chaleur à différentes températures, et pour tous types de compresseurs. Les trois axes d’économies d’énergies sont la régulation, le contrôle digital, la récupération. En parallèle encore, d’autres innovations allant dans le sens de la réduction de l’empreinte carbone sont en cours.
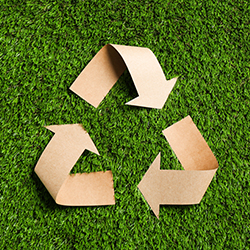
3) Environnement : gestion des déchets et technologies éco-responsables.
Sur les marchés de l’air comprimé, la grande majorité des compresseurs sont lubrifiés par injection d’huile ou par bain d’huile. Leur utilisation génère des déchets produits sous forme de résidus d’huile. Résidus d’huile dans l’air ambiant dans le cas des compresseurs à injection d’huile, résidus d’huile dans les cartouches filtrantes, ou encore de condensats contaminés. Il faut encore compter sur l’élimination des composants usés du compresseur, puis in fine de l’élimination du compresseur complet après 10 ans.
Dans le cas des compresseurs sans huile, il existe trois types de technologies, les pistons industriels, les rotatifs et les unités centrifuges. Les déchets produits par les compresseurs sans huile sont moindres, car le condensat est de l’eau pure, les filtres ne sont pas contaminés par l’huile et il n’y a pas de changement d’huile toutes les 2000 heures.
La gamme AF basse pression à piston sans huile, offre des intervalles de service très longs, de 8000 à 16000 heures, ce qui réduit au minimum les déchets provenant de l’usure des composants. Les joints doivent être remplacés sur le deuxième étage toutes les 8000 heures et sur le premier étage toutes les 16000 heures. Les vannes, pour garantir un haut rendement, sont également remises à neuf après 8000 heures pour le deuxième étage et 16000 heures pour le premier étage.
Ateliers François et ses filiales améliorent continuellement la gestion des ressources naturelles par le recyclage, le tri et la réduction des déchets sur leurs équipements selon les normes régionales et nationales en vigueur. Une déclaration annuelle avec chiffrage est remise annuellement à l’institution belge Valipac, de manière biannuelle à Statbel.
L’ensemble de l’éclairage est également passée en led dans son entièreté. Des projets de récupération de chaleur ainsi que de récupération d’eau sont également en cours.
Parallèlement à la construction de récentes installations à Alleur- Liège, AF a investi dans la technologie pour permettre une source d’énergie durable de 200 kW de puissance électrique, ce qui représente la consommation moyenne annuelle de 300 ménages européens.
Lire le AF’s Code of Conduct, Legal, Ethical & Social Commitments